Validation and validation of clean room (clean room validation)
Definition of clean room validation
A clean room is a modular environment where the following environmental factors are controlled:
Temperature, airborne particles, microbial load, relative humidity, pressure difference, barometric pressure and air flow.
Validation of clean room is done for various reasons. Among the most important reasons for which authentication is needed, the following can be mentioned:
- Ensuring that the design of the clean room components is suitable for its intended purpose.
- Ensuring that facilities, equipment and environment are in accordance with user requirements (URS);
- The facilities, equipment and environment comply with the legal requirements defined in that country.
- The facilities, equipment and environment work together as a system to meet the defined standards.
Clean rooms are first validated and then a certificate is issued based on the selected class mentioned in the ISO 14644 standard. Each class of clean room has its own unique requirements, based on its classification, special facilities should be built.
Cleanroom Accreditation Lifecycle
Cleanroom validation follows a specific life cycle. The life cycle consists of four phases, each of which performs specific tasks to control changes in the modular environment. In general, the work of validating the clean room is done in four phases; It starts with the design control phase and ends with the cleanroom performance validation. Changes in the equipment and control factors after the validation of the clean room are grounds for re-validation of the clean room.
First phase: DESIGN QUALIFICATION
Cleanroom validation begins with Design Quality Assurance (abbreviated as DQ from now on). The purpose of this step is to prove through objective evidence that the design is suitable for its intended purpose. Design quality assurance is an exercise to verify the requirements defined in the acceptance criteria section. Acceptance criteria are specified explicitly or implicitly by the employer at the beginning of the job. These criteria should be defined in your DQ protocol; Therefore, the DQ protocol must consider the following:
- User Required
- Specifications (URS)
- Documents and details of the seller
- Equipment arrangement
- Purchase orders for various equipment
- Design documentation
- Factory Acceptance Tests (FAT)
- Construction plans (As Build)
- Data Sheets
The output of the design quality assurance phase is a report from this phase according to a standard document listing (SDL) file that documents the following:
- Design requirements
- Tender requirements
- Purchase and order documents
- List of documents provided by the seller
- Construction plans
- List of components, equipment and parts used
- Checklists
- Factory acceptance tests
After verifying the quality of the design, it is possible to proceed to the installation stage of equipment and air conditioners, etc. The DQ stage is considered a prerequisite to start the installation quality assurance (IQ) stage.
Second phase: INSTALLATION QUALIFICATION
The purpose of this stage is to verify the quality of installation of equipment, air conditioners, panels, doors, etc. (we call this stage IQ for short). In the stage of installation of clean room equipment, we act through “confirmation”. That is, the equipment – as installed – must meet user requirements and design requirements. The IQ phase focuses on the following, which should be detailed in your IQ protocol:
- HVAC calibration
- P&ID loop verification
- HEPA filter integrity test data review
- Critical equipment calibration status
- Clean room installation site acceptance tests (SAT)
- Quality assurance tests for equipment installation and…
- System standard operating procedures and work instructions
The output of this step should be a detailed and highly detailed IQ report that addresses all of the above elements, as well as a written file that documents the following elements:
- Project changes
- Taking IQ tests
- calibration
- Documents provided by suppliers
- Equipment certificate
- Deviations created during installation
- Clean room site acceptance tests (SAT)
- List of consumables, installed equipment, material flow chambers, etc.
- Environmental survey report
Installation quality assurance (IQ) is a prerequisite to start the operational quality assurance (OQ) phase.
The third phase: OPERATION QUALIFICATION
The purpose of this phase is to verify operational quality (OQ), which is to demonstrate through objective evidence that the cleanroom is operating in accordance with the design requirements and user-defined requirements and is operating within specified and acceptable limits.
In the OQ protocol, the following should be considered:
- HVAC system performance testing based on specific performance requirements
- Critical alarms (alarms that should be generated by the clean room monitoring system in emergency situations)
- Interlock alarms
- Critical operating parameters defined in the cleanroom data sheet
- Filter integrity tests
- Standard performance for clean room
- Air speed and air flow
- Airflow patterns
- pressure difference
- Levels of suspended particles in the air
- Amount of particles on surfaces
- relative humidity
- Temperatures
- Sound measurement
- Ambient light measurement
- Clean room recovery test
The OQ phase should also deal with “Worst Case” scenarios. To design a “worst case scenario” for cleanroom performance, critical operational parameters are identified from cleanroom data information. Operating range as well as critical range for each parameter should be designed and documented. These should include the following items:
- Maximum and minimum temperature
- Maximum and minimum humidity
- Personnel contamination
“Worst case scenario” is usually done at maximum and minimum parameters.
The output of this step is a written report called an OQ that addresses alarms and cleanroom performance requirements specified by the user.
The fourth phase: PERFORMANCE QUALIFICATION
The purpose of cleanroom performance quality assurance (abbreviated as PQ) is to demonstrate with objective evidence that the cleanroom is consistently operating within defined parameters to produce a defined and desired environmental outcome. Cleanroom performance qualification includes testing and monitoring the following:
- Levels of suspended particles in the air
- Amount of particles on surfaces
- Microbial load
- relative humidity
- pressure difference
- Temperatures
- Sound measurement
- Ambient light measurement
The output of the PQ phase is a written and documented report that analyzes cleanroom performance using equipment parameters. PQ is a prerequisite for certification.
CLEANROOM certificate
Certified clean rooms are known as “clean class or clean room class”. Therefore, clean rooms are approved based on “cleanliness class”. The level of cleanliness chosen is determined by the user’s needs. Cleanroom classes are defined in ISO1464. At least these ten tests must be passed in order to issue a “room cleanliness class” certificate:
- Airborne particle counting test
- Air flow test
- Air pressure difference test
- Filter leakage test
- Air flow visualization test
- Air flow direction test
- Temperature test
- Moisture test
- Recovery test
- Chamber leak test
- Sound measurement
- Ambient light measurement
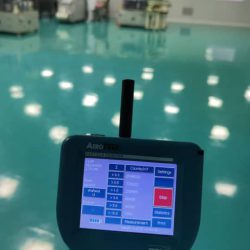
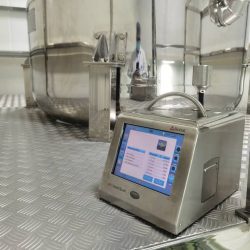
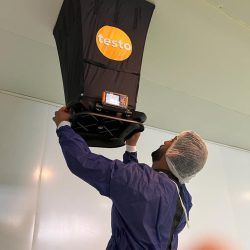
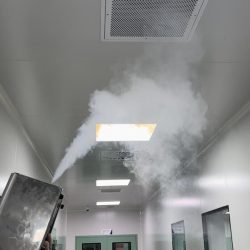
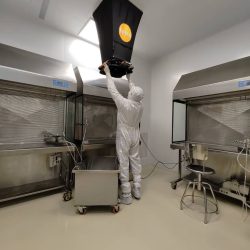
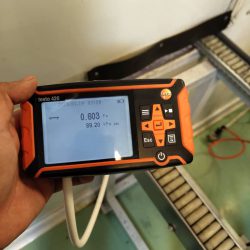
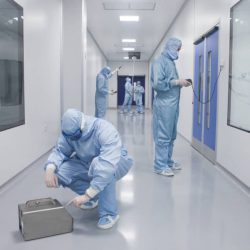